Summary:Auto lamp injection moulding is a process used to produce auto lamps, which are the most vital components of automobiles' lighting systems. The process involves the creation of a mould that is used to produce a series of identical auto lamp parts by ......
Auto lamp injection moulding is a process used to produce auto lamps, which are the most vital components of automobiles' lighting systems. The process involves the creation of a mould that is used to produce a series of identical auto lamp parts by injecting molten plastic into the mould. The mould is designed to take the shape of the final product, and the injection process is performed under high pressure to ensure that the plastic fills the mould completely. Once the injection process is complete, the mould is cooled, and the plastic solidifies, forming the auto lamp component. This process has numerous advantages over other manufacturing processes, including its speed, consistency, and cost-effectiveness.
The first advantage of auto lamp injection moulding is its speed. The process is very fast, with each injection cycle taking only a few seconds to complete. This allows manufacturers to produce large quantities of auto lamps within a short period, reducing production times and increasing productivity. Furthermore, the process is highly automated, which further improves its speed and efficiency.
The second advantage of auto lamp injection moulding is its consistency. Because the process is highly automated, the parts produced are highly consistent, with very little variation between parts. This ensures that the auto lamps are of high quality and meet the required specifications. Additionally, the process is highly repeatable, which means that the same quality can be achieved over and over again, even when producing large quantities of auto lamps.
The third advantage of auto lamp injection moulding is its cost-effectiveness. Because the process is highly automated, it requires less labour and human intervention, which reduces labour costs significantly. Additionally, the process is highly efficient, with very little material waste, reducing material costs. Furthermore, because the parts produced are highly consistent, there are fewer rejects and less rework required, reducing the overall cost of production.
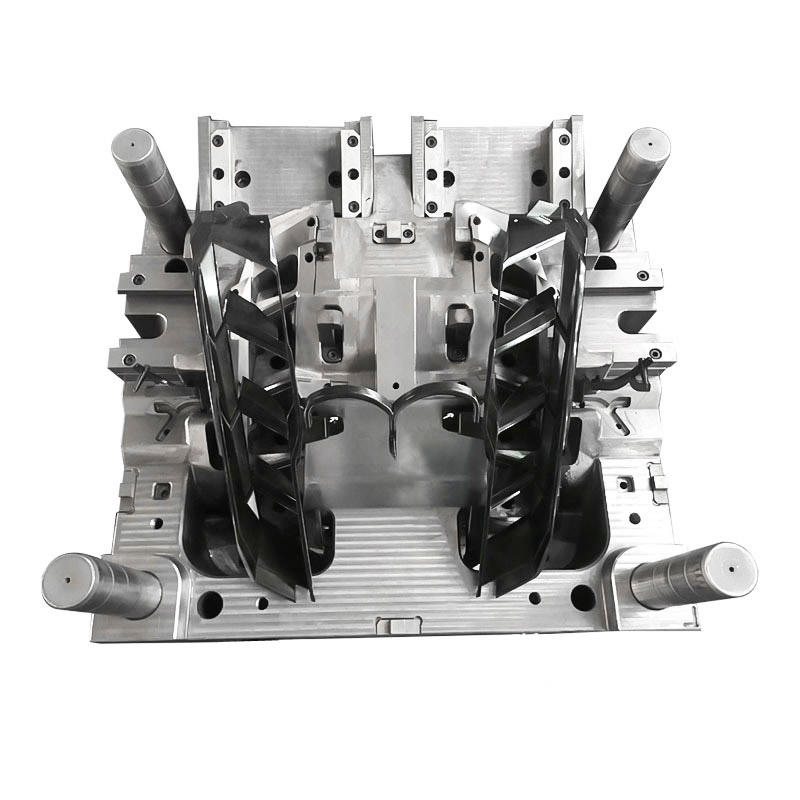