Summary:Car light molding is a technique used in the manufacturing of car lights that enhances their durability and functionality. This process involves the injection of molten plastic material into a mold, which then hardens and forms the desired shape. Car......
Car light molding is a technique used in the manufacturing of car lights that enhances their durability and functionality. This process involves the injection of molten plastic material into a mold, which then hardens and forms the desired shape. Car light molding is an important step in the production of high-quality car lights that meet the stringent safety standards set by regulatory agencies.
Car light molding has revolutionized the car light industry by providing a more efficient and cost-effective way to produce car lights. In the past, car light manufacturers had to rely on traditional manufacturing techniques such as hand-molding, which was a time-consuming and expensive process. With car light molding, manufacturers can now produce large quantities of car lights in a fraction of the time it would take using traditional techniques.
The use of car light molding has also led to improvements in the quality of car lights. The injection molding process ensures that each car light is consistent in size and shape, which helps to improve the overall performance of the car light. The technique also allows for the integration of additional features into the car light, such as LED lights, which were not possible with traditional molding techniques.
Car light molding is a highly specialized process that requires expertise and precision. The process begins with the creation of a mold, which is typically made of steel or aluminum. The mold is designed to the exact specifications of the car light, including its shape and size. Once the mold is created, it is placed into an injection molding machine, which heats the plastic material to a high temperature and injects it into the mold. The plastic material then cools and hardens, forming the shape of the car light.
There are several different types of plastic materials that can be used in car light molding, including polypropylene, polycarbonate, and acrylic. Each type of material has its own unique properties, which make it ideal for certain applications. For example, polycarbonate is a highly durable material that is often used for the lenses of car lights, while acrylic is a more lightweight material that is often used for the outer shell of the car light.
In conclusion, car light molding is a critical process in the production of high-quality car lights. It has revolutionized the car light industry by providing a more efficient and cost-effective way to produce car lights while also improving their overall quality and functionality. The process requires expertise and precision, and manufacturers must carefully choose the right plastic materials to ensure that the car lights meet the necessary safety standards. As the car industry continues to evolve, car light molding will remain an essential process for the production of high-quality and safe car lights.
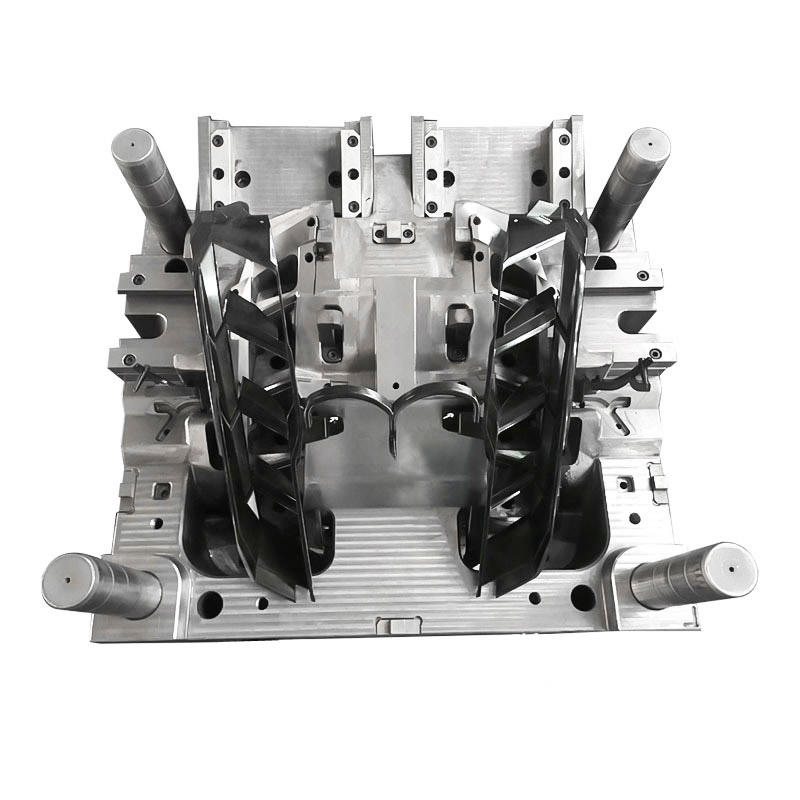