Summary:Crate mould technology has revolutionized the storage and transportation industry by providing durable and efficient solutions for packaging and logistics. Crates, once simple containers, have undergone a significant transformation through advancemen......
Crate mould technology has revolutionized the storage and transportation industry by providing durable and efficient solutions for packaging and logistics. Crates, once simple containers, have undergone a significant transformation through advancements in moulding techniques and materials. These innovations have resulted in the creation of sturdy, versatile, and cost-effective crates that meet the evolving needs of various industries.
Traditionally, crates were made from wood or metal, which had limitations in terms of durability, weight, and design flexibility. However, with the introduction of injection moulding, manufacturers can now produce crates using high-quality plastics. Injection moulding involves injecting molten plastic into precisely designed moulds, resulting in crates with exceptional strength, consistent quality, and enhanced functionality.
One of the key advantages of crate mould technology is the ability to create crates with intricate features and designs. Manufacturers can incorporate reinforcements, handles, stacking features, and locking mechanisms seamlessly into the mould design. These additions enhance the usability and efficiency of the crates, allowing for easy handling, secure stacking, and efficient utilization of storage space.
Moreover, the use of advanced materials such as polypropylene (PP) and high-density polyethylene (HDPE) has further elevated the performance of crate moulds. These materials offer excellent impact resistance, durability, and resistance to chemicals and moisture. As a result, the resulting crates can withstand harsh environmental conditions, ensuring the safe storage and transportation of goods.
The customization possibilities enabled by crate mould technology have also played a crucial role in meeting the diverse needs of various industries. Manufacturers can tailor the size, shape, and load capacity of crates to suit specific requirements. Whether it's for automotive parts, electronics, agricultural produce, or general goods, crates can be designed and manufactured to provide optimal protection and organization during storage and transportation.
In addition to their functionality, crate moulds have contributed to sustainable practices in the packaging industry. Plastic crates are reusable and recyclable, reducing the environmental impact associated with single-use packaging materials. The durability of crate moulds ensures a longer lifespan for the crates, resulting in reduced waste generation over time.
Furthermore, the implementation of automation and digital technologies in the crate moulding process has increased production efficiency and reduced costs. Computer-aided design (CAD) software allows for precise and rapid development of mould designs, optimizing the manufacturing process. Automation and robotics in moulding facilities enable faster production cycles, consistent quality, and cost-effective operations.
The versatility of crate moulds extends beyond traditional storage and transportation applications. Innovative industries have found alternative uses for crates, such as modular furniture, garden planters, and retail displays. The adaptability and robustness of these moulded crates make them ideal for repurposing, further extending their lifespan and reducing waste.
As industries continue to seek efficient and sustainable packaging and logistics solutions, crate mould technology remains at the forefront of their operations. The ongoing advancements in moulding techniques, materials, and customization options have transformed crates into indispensable assets for businesses worldwide. With each innovation, crate moulds continue to shape the way we store, transport, and organize goods, offering reliable, durable, and eco-friendly solutions for various industries.
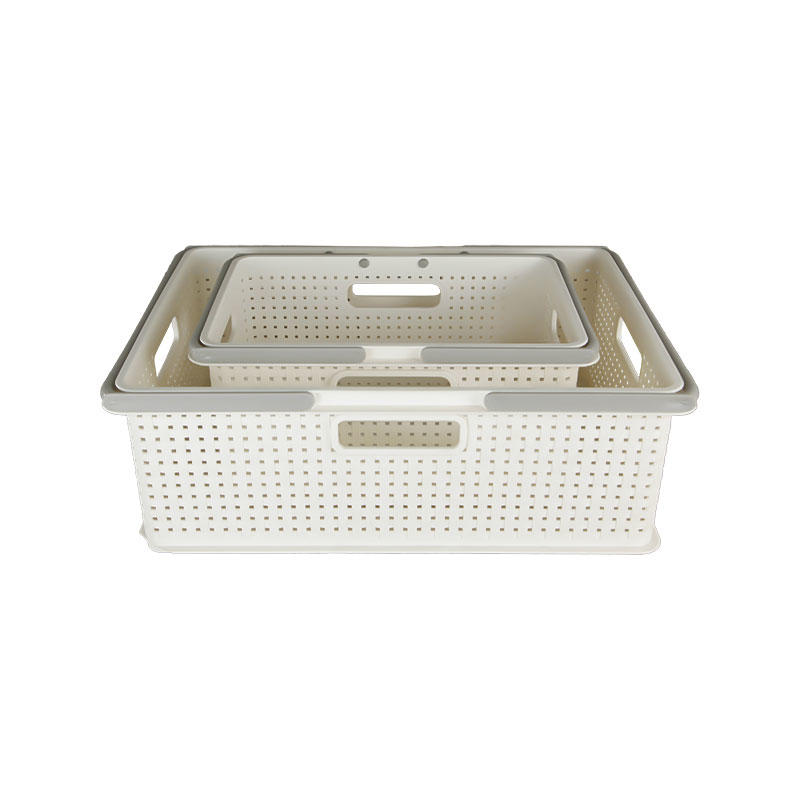