Summary:In a constant pursuit of improving vehicle safety and aesthetics, the automotive industry has witnessed significant advancements in car bumper mould technology. Car bumpers, once considered mere protective shields, have evolved into integral componen......
In a constant pursuit of improving vehicle safety and aesthetics, the automotive industry has witnessed significant advancements in car bumper mould technology. Car bumpers, once considered mere protective shields, have evolved into integral components that combine functionality, design, and manufacturing precision. The latest innovations in bumper moulds have not only enhanced crashworthiness but also contributed to the overall appeal of modern vehicles.
Traditionally, car bumpers were made from metals such as steel, which offered durability but lacked flexibility. However, with the advent of advanced polymers and composite materials, manufacturers have been able to develop lightweight yet robust bumper systems. This shift has been made possible due to the advancements in bumper mould technology, enabling the production of complex shapes and designs with increased efficiency and precision.
One of the key breakthroughs in car bumper mould technology is the utilization of injection molding techniques. This process involves injecting molten plastic or composite materials into a specially designed mould cavity. The resulting bumper components exhibit high strength-to-weight ratios, improved impact absorption capabilities, and enhanced resistance to corrosion and environmental factors. Injection molding allows for the seamless integration of various functional features, such as sensors, fog lights, and parking assistance systems, into the bumper design.
Moreover, the introduction of additive manufacturing, commonly known as 3D printing, has opened up new possibilities in bumper mould production. This technology enables the fabrication of highly complex moulds with intricate details and geometries that were previously difficult to achieve using traditional manufacturing methods. 3D-printed bumper moulds allow for faster prototyping, reduced production costs, and increased design flexibility, facilitating rapid innovation in the automotive industry.
In addition to safety considerations, car bumper mould technology has also played a significant role in enhancing vehicle aesthetics. Manufacturers can now create bumpers with sleek contours, unique textures, and seamless finishes, thereby contributing to the overall visual appeal of automobiles. The ability to incorporate personalized design elements has allowed automakers to differentiate their vehicles in a competitive market.
As automotive manufacturers continue to prioritize vehicle safety and design, the evolution of car bumper mould technology remains a critical aspect of their development process. The ongoing advancements in materials, manufacturing techniques, and simulation tools have propelled the automotive industry toward producing safer, lighter, and more visually appealing vehicles. With each innovation, car bumper moulds continue to redefine the way we perceive and interact with automobiles, paving the way for a future where safety and style go hand in hand on the roads.
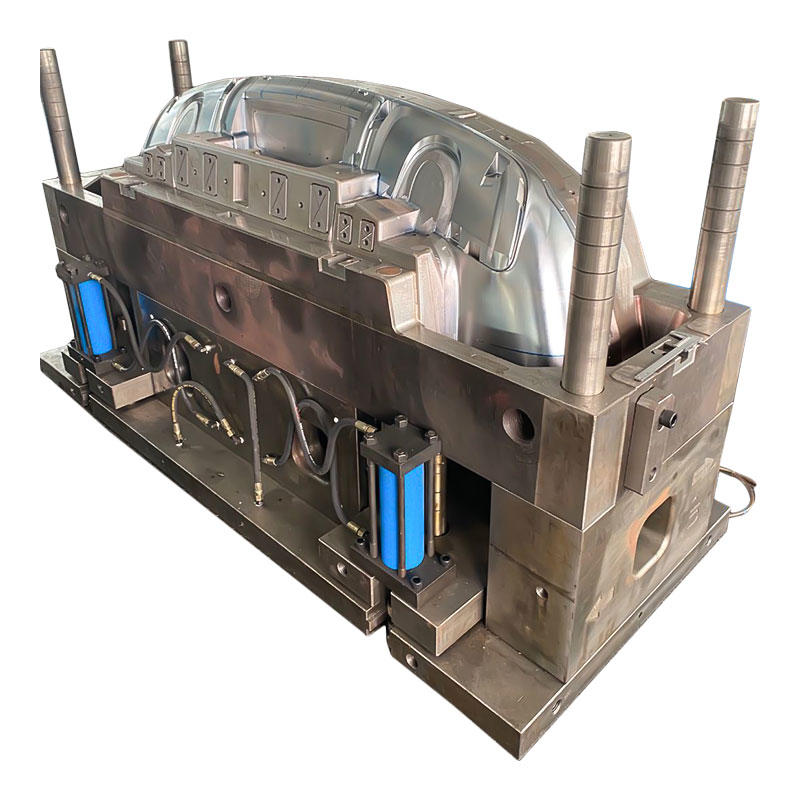